Revolutionizing Warehouse Operations with IMS
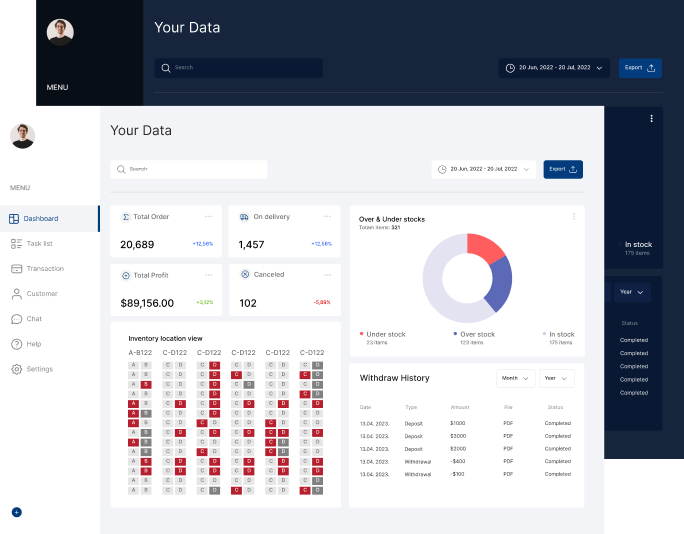
Introduction
In today’s business world, efficient warehouse management is key to success. It ensures timely deliveries, proper inventory levels, and smooth operations.
However, many small to medium-sized businesses struggle with outdated paper systems, causing mistakes and inefficiencies.
This case study delves into how a company overcame this hurdle by implementing an Inventory Management System (IMS) to improve its warehouse procedures.
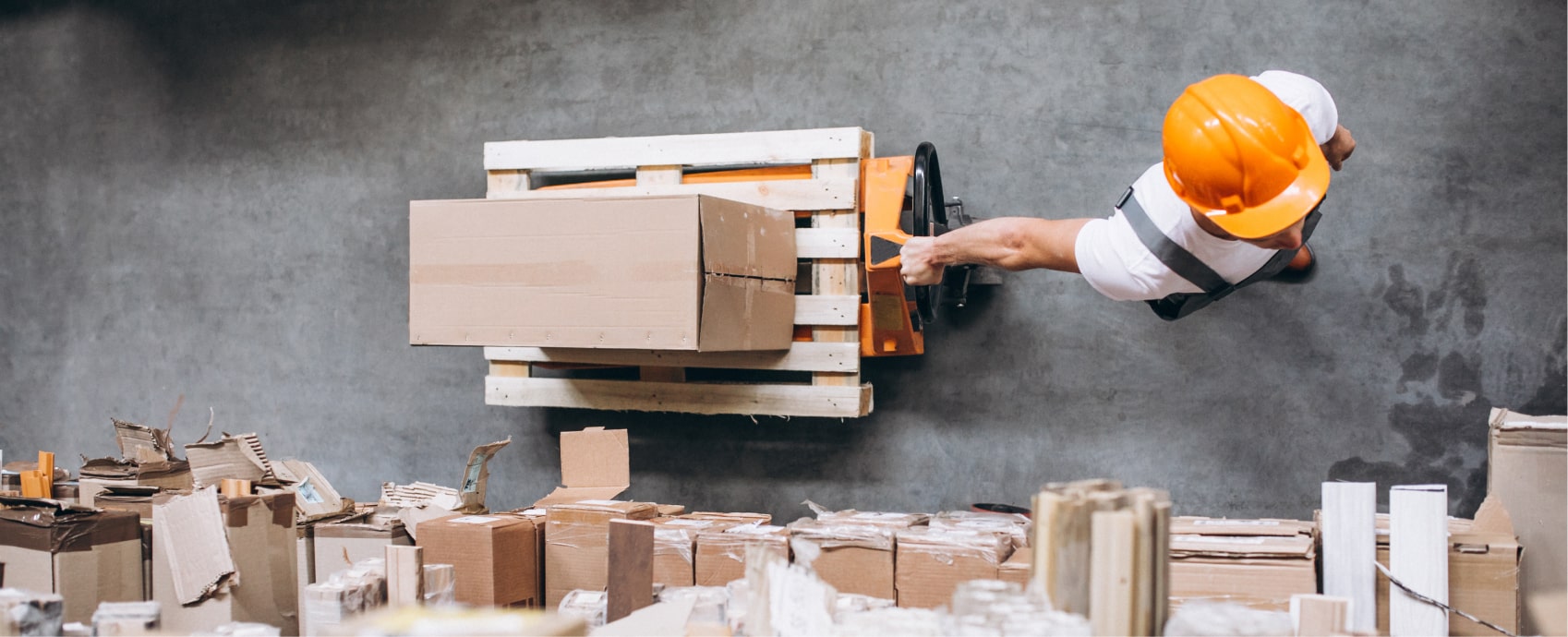
Challenges
Delayed Deliveries:
Manual scheduling caused significant delays due to high order volumes.
Missed Deadlines due to Improper Palletization:
Inadequate palletization led to goods expiring and big financial losses.
Excessive Empty Space:
Poor distribution of goods left a lot of empty space, wasting warehouse capacity.
Handmade Stickers Errors:
Manual labeling caused many errors, leading to packages being sent to the wrong addresses.
Solution
Our proposed solution was implementing an interactive Inventory Management System (IMS) tailored for small and medium-sized enterprises undergoing digital transformation.
This system provides real-time information, efficient inventory management, and streamlined operations. It is customizable and comes with a structured process of assessment, customization, training, and ongoing support for a smooth transition.
Results
Swift Delivery:
By implementing automated order processing, we achieved remarkable improvements in delivery speed and accuracy. This innovation not only saved valuable time and resources but also significantly reduced errors. As a result, the company's productivity surged by an impressive 318%.
Better Palletization:
Our strategy for optimizing palletization focused on prioritizing goods nearing expiration. This proactive approach significantly minimized product losses and associated expenses. Over the course of a year, the company saved over 2 million euros by reducing waste and direct costs linked to expired goods.
Optimized Space:
The implementation of an algorithm for efficient goods distribution upon arrival at the warehouse unlocked substantial space savings. By redistributing items more effectively, we increased available warehouse space by 18-19%. This optimized use of space not only allowed for better organization and storage but also opened up opportunities for increased profitability.
Reduced Labeling Errors:
Our automated barcode label printing solution dramatically reduced labeling errors. By cutting error rates by over 15%, we significantly lowered transportation and parcel return costs. This improvement streamlined operations and enhanced overall efficiency.
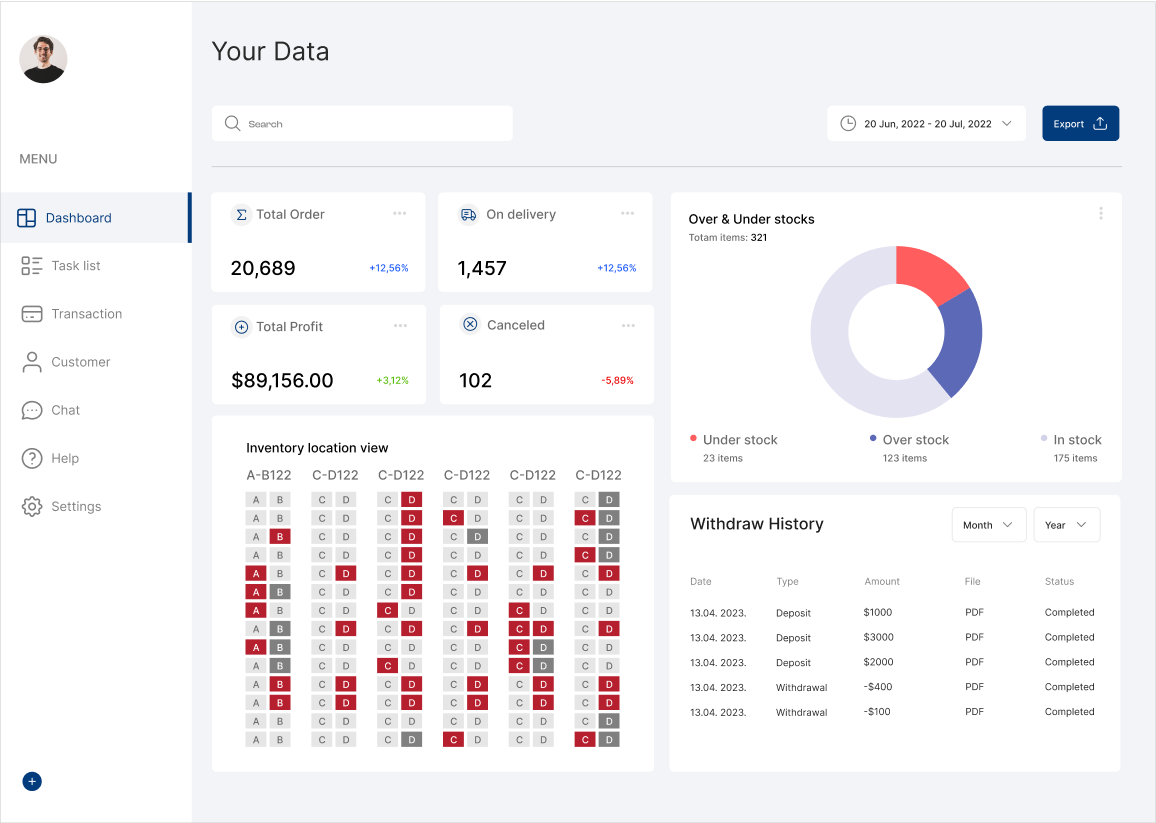
See what our clients have to say about their experience with us.
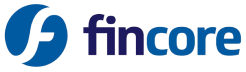

Final word
Through embracing IMS, our client smoothly transitioned from manual paper-based methods to a digital warehouse management solution.
They improved operational efficiency, accuracy, and scalability, while reducing costs caused by inefficiencies.
This transformation not only set them up for growth but also increased their competitiveness, showing the power of digital advancements in warehouse management.